Analysts have been raving about how mining companies are set to record bumper increases in revenue due to rising global commodity prices. But that notion is based on the assumption that key elements in critical phases like mineral processing have been followed to the hilt.
The objectives of increasing grades and recoveries of mineral aggregates environmentally friendly, safely and cost effectively would have been scrupulously implemented. Yet, in reality, missteps (poor planning and execution) in the filtration processes could be the difference between increase and reduction in revenue. As far as filtration goes, fine margins can make a huge difference.
Reports indicate that even the use of advanced filtration technologies such as decanter centrifuges, screw presses and belt presses, amongst others, does not offset poor implementation of filtration. Unfortunately, moisture levels that do not meet the threshold (low or high) are frequently encountered. Most often, this is attributable to overlooked factors that impair the process of filtration. So, if mining companies are to achieve efficient filtration, they have to seek sustainable ways of managing these methodically. And one of the sure-fire techniques is the proper use of chemical dewatering agents in filtration processes. Chemical dewatering agents – which include surfactants, flocculants, polymers, sulfonates, and sulfates – are mostly used to control moisture levels and increase throughput in filter applications. That is why mining companies must be more particular about the nature of the dewatering agents and the way they apply them (dose).
Why chemical dewatering agents have become important
There is increased obligation on mining companies in the way they undertake their filtration processes. This is due to the rising cost in operating costs which is impacting on, growing scarcity of viable ore bearing rock, in addition to stringent environmental laws and regulations.
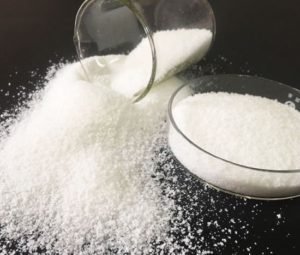
- Cost effective application and efficiency
Mining companies can only make the most of their rising global commodity prices if they improve efficiency and contain costs. However, the rising oil prices, as a result of the Ukraine War will offset any envisaged increase in profit.
Another noteworthy aspect is that skyrocketing energy costs lend more credence to the need for sound application of filtration processes. This is considering that filtration is an energy-intensive process. When poorly implemented, the process results in consumption of more energy, which translates in further expenditure.
This necessitates that mining companies leave no stone unturned in their efforts to improve efficiency and contain costs from every available avenue. One of the available avenues, as regards filtration, would be in the sound application of chemical dewatering agents.
- Environment Social and Governance (ESG)
Environment Social and Governance (ESG) is no longer an option but an integral part of their operations, with points earned from sound reporting used as a factor in determining access to capital. ESG regulations and rules bind mining companies to be accountable for the impact of their activities on the environment, host communities, and adhere to good governance values. Pertaining to environmental friendliness, disposal laws stipulate sustainable measures governing the disposal or reuse of sludge. Usually, untreated or inadequately treated sludge contains organic chemicals, toxic metals, chemical irritants and pathogens, which may cause several diseases. When disposed of, the waste disrupts aquatic life and poses serious health hazards in water bodies.
READ: Tanzania inaugurates drinking water plant in the Coast Region
Alternatively, the use of technologies that leave a small footprint on the environment is highly recommended. For instance, from a filtration perspective, using a more environmentally friendly (less hazardous) chemical dewatering agents would be preferrable to xanthates. Xanthates include sodium ethyl xanthate (SEX), sodium isopropyl xanthate (SIPX), sodium isobutyl xanthate (SIBX) and potassium amyl xanthate (PAX).
- Health and safety
Xanthates may be effective in keeping moisture at a normal level, but they may pose health and safety risks. Studies conducted in various countries show the dangers of Xanthates exposure to human health.
Moreover, there is a high safety risk attached to high moisture content of transported mineral products (commonly called Transportable Moisture Level (TML)). When a ship is carrying ore with a high moisture content (beyond the TML), there is always a risk of foundering. In the past 30 years, at least 24 accidents that occurred were attributed to cargo liquefaction.
Mistakes in dewatering application
For effective filtration, mining companies have to identify the common lapses that impair filtration and result failure to meet moisture level targets. More often than not, the following factors have an impact on the outcome – changes in feed rate (fluctuations on the milling feed rate and grinding media), chemical and mineralogical composition or particle size distribution. The ensuing dewatering deficiencies can impede the subsequent processing steps. A case in point is in iron ore pelletising operations, where moisture levels below 9% are required for pellet formation. Too much or too little water creates a narrow moisture range for optimal process conditions. With reference to the particle size distribution, small particle size becomes increasingly difficult to dewater.
In order to address these challenges, a mining company may be prompted to increase capital expenditure (CAPEX) or additional resource allocation towards process modification to have additional or larger filtering capabilities. In most cases, the scenarios are not predicted earlier in the design. Above and beyond, while this task is being carried out, there would be operational downtime, resulting in loss of productivity.
Addressing dewatering shortcomings
Addressing dewatering shortcomings can either pose a challenge or an opportunity, depending on how a mining company handles it.
There is a saying which goes, “A bad carpenter blames their tools”. Most often, dewatering failure, which is reflected in high moisture content, is as a result of poor selections and execution of processes. This is considering that there are complex variables associated with dewatering.
Demonstrably, the targeted level of dewatering mineral aggregates is attainable where the feed rate is consistent, particle size distribution and mineralogical composition. Nevertheless, it has been consistently proven that the proper use of chemical dewatering agents is a viable option to keep production stable during periods of challenging scenarios in dewatering.
For dewatering aids to produce the desired output, precision is critical. Chemical dewatering agents should be applied at correct points. This is given that different dewatering aids have varied processes and intensities, which considerably affect the performance of mineral sludge dewatering.
Numerous gains
There are numerous gains from correct use of chemical dewatering agents in mineral aggregate filtration. Dewatering agents ensure a predictable, cost-effective operation where there is little to no requirement for CAPEX or additional resource allocation. Also, achieving moisture target – reaching the dewatered state – is within shorter cycle times, increasing filtering productivity.
Generally, what a mining company gets from a chemical dewatering agent is an operational resource that enables a safer, stable and reliable process, with noticeable reduced production costs through filtration. Effective filtration is one of the avenues available at the disposal of mining companies to ensure that they make the most of high commodity prices.